Process development and production
Pilot units are the intermediate link between laboratory and industrial scale distillation units. The main aim of pilot scale distillations is to generate data for scale-up and process development. Moreover our pilot systems can be used for production of small product quantities as well. Experience, gained by experiments with a variety of products on our own pilot plants, has influenced the design and continuously improves the quality and performance of our systems.
Why pilot units?
Verification of the results of the laboratory tests under real process conditions
Determination of design parameters for a future industrial scale distillation system
Scale-up for process equipment and aggregates of the industrial plant
Monitoring of product properties during distillation (color, foaming, fouling etc.)
Production of samples up to several metric tons
Required raw material quantities about 20 – 400 kg
MOC of evaporator: stainless steel
- Capacity: 3 kg/h up to 100 kg/h
- Evaporator size: 0,06 m² - 0,5 m²
- Heating temperature: max. 350 °C (by thermal oil) - inductive heating for higher temperatures on request
- Operating pressure :
- min. 0,1 mbara for Wiped Film Evaporator
- min. 0,001 mbara for Short Path Evaporator
- Material of construction: stainless steel and special materials
- Low product hold up in pipes and vessels
Standard Set-up
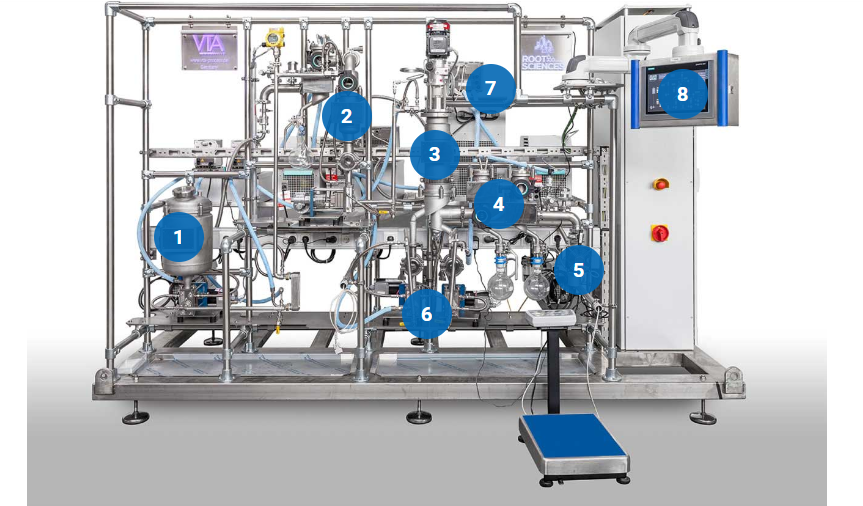
1. Feed
2. Degassing stage
3. Short Path Evaporator
4. Cold traps
5. Vacuum system
6. Discharge systems
7. Heating and cooling systems
8. Control system
The design of our distillation systems is based on our customers´ requirements and product properties.
The following options can be considered for our tailor-made systems:
- Evaporator types: Wiped Film, Short Path, Horizontal Thin Film
- Different wiper systems
- Fractional distillation systems
- Continuous feeding and discharge options
- Trace heating and tempering
- Material selection (product wetted)
- PLC and visualization option
- Multi-stage and combined distillation systems